Our Blogs
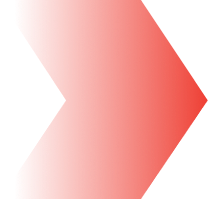
Home / Blogs
All Blogs
All Chemical Reports
CAPB Report
Chemical Market
Chemical Sourcing
Citric Acid Report
Flavours and Fragrances
Food and Nutrition
Intermediates and Solvents
News
Nonyl Phenol Ethoxylates Report
Paints and Coatings
Personal Care
SLES Report
Supply Chain
Technology and Digitisation
Featured Blogs

Minimum Order Quantity Strategies: Reducing Lead Time Without Compromising Profitability
Elchemy
•
8th Jul 2025

What Is a Distributor of Specialty Chemicals and How to Choose the Right Specialty Chemical Suppliers
Elchemy
•
8th Jul 2025

What Is Silver Nitrate Used For and Where Elchemy Fits In the Value Chain
Elchemy
•
5th Jul 2025
Chemical Market

What Is a Distributor of Specialty Chemicals and How to Choose the Right Specialty Chemical Suppliers
Elchemy
•
8th Jul 2025

What Is Silver Nitrate Used For and Where Elchemy Fits In the Value Chain
Elchemy
•
5th Jul 2025

Uses for Methyl Ethyl Ketone and Elchemy’s Role in Supplying Industrial-Grade MEK with Technical Support
Elchemy
•
5th Jul 2025
Personal Care

Comparing Benzyl Alcohol and Benzoyl Peroxide: Functional Differences in Personal Care Products
Elchemy
•
4th Jul 2025

Top 10 Uses for Bentonite Powder Across Industries: From Skincare to Drilling
Elchemy
•
4th Jul 2025

Top Industrial Applications of Benzyl Alcohol in Personal Care and Cosmetics
Elchemy
•
2nd Jul 2025