At a Glance:
Protective coatings, specifically those used in the industrial sector, play a very crucial role in extending the life of materials, especially metals, within harsh environmental conditions. These are protective coatings which protect the surface from corrosive elements, such as moisture, chemicals, and temperature variation. Various chemicals, including epoxy-based coatings and coatings, are included in these protective layers to maximize resilience and resist corrosion. We will discuss in this blog how different chemicals contribute to protective coatings’ anticorrosive properties, keeping in mind their properties and applications based on the exposure of industry as well as the environment.
What is Industrial Coating?
Protective industrial coatings refer to specific paints or coatings provided over surfaces to protect them from corrosion, wear, or other environmental destructive effects. In addition to shielding surfaces against harm, protective coatings may also offer aesthetic and functional benefits, for instance, enhancing the appearance of non-slip surfaces, but the most important function that protective coatings play in so many industries is to enhance corrosion resistance, especially in very hostile environments such as oil rigs, chemical plants, and manufacturing facilities.
Industrial paints, varnishes, and epoxy-based systems are examples of protective coatings. Chemicals in industrial paints are manufactured with the primary concern to avoid corrosion as well as to create a barrier between the surface and the surrounding environment. That’s why epoxy-based coatings are applied so widely – good adhesion with a certain level of toughness and chemical resistance.
What Leads to Corrosion in Harsh Environments?
Corrosion is a natural process where metals lose their integrity by reacting with the elements associated with the environment, like oxygen, moisture, and chemicals. In industry, being exposed to what are essentially harsh environments, such as a marine or chemical plant environment, corrosion will severely damage equipment, machinery, and infrastructure. Contributing factors include:
- Moisture: The presence of water or moisture leads to rusting, especially if it is an iron or steel material.
- Salts and Chemicals: The use of salts or aggressive chemicals in a seaway or chemical industries accelerates corrosion as well.
- Temperature Extremes: High temperatures weaken the material and render it susceptible to chemical reactions.
- Mechanical Stress: Materials under mechanical stresses have a good chance of cracking, thus exposing the metal to corrosive elements.
Such factors are considered in protective coatings, particularly those that utilize epoxy-based coatings paints and coatings; they prolong the lifetime of materials operating within corrosive environments.
Role of Chemicals in Enhancing Resistance to Corrosion
Industrial coatings or paints are able to provide effective corrosion protection through the use of specific chemicals in their preparation. Such important chemicals that improve corrosion resistance include:
Resin Epoxy
Industrial epoxy resins have the highest usage in protective coatings and display excellent adhesion and chemical resistance with great durability. Coatings based on epoxy create an extremely tough and impermeable barrier of protection for the coated surface against moisture, salts, and aggressive chemicals. That is why epoxy-based coatings are highly resistant to chemical attacks and are often used in chemical plants, oil and gas pipelines, and offshore platforms.
Benefits of epoxy-based protective coatings:
- Good Adhesion: The Epoxy resins have a strong bond to various substrates, guaranteeing that the protective coat adheres even under extreme conditions.
- Chemical Resistance: Epoxy resins are strong chemical resistant and, therefore, unaffected by acids, alkalis, and many solvents. Epoxy resins are good for applications wherein the industries involve work with highly aggressive chemicals.
- Thermal Stability: Epoxy resins can resist high temperatures while the protective property of the paints is retained even when the thermal conditions change.
Zinc-Rich Primers
Zinc-rich primers are another industrial coating that adds protection against rust by being sacrificial. As it is more reactive than steel, it would consume itself to protect the material, which has been said to be cathodic protection. After it has been applied to the steel, the zinc-rich primer forms a protective layer over the entire steel surface, even after it has been scratched or coated.
Key Benefits:
- Sacrificial Protection: Zinc consumes itself as a sacrificial agent to protect the steel from rust formation.
- Long-Term Durability: The primers that are zinc-rich offer protection for very long periods, especially for aggressive environments that include marine or industrial plants.
- Compatibility with Top Coats: They can also topcoat over an epoxy or polyurethane topcoat to form a multi-layered protective system.
Polyurethane Coatings
Polyurethane coating provides good flexibility and abrasion resistance. Thus, it suits applications where mechanical wear and tear can be anticipated. Polyurethane is not very good in terms of chemical resistance when compared to epoxy, but it provides good protection in terms of UV protection that prevents the degradation of the coating outdoors.
Benefits of Polyurethane Coatings
- UV Resistance: Protection against sunlight, and hence, polyurethane coatings are highly suitable for outdoor applications.
- Flexible and Impact-Resistant: This polyurethane is flexible, meaning it minimizes cracking or peeling in a stressful environment due to a mechanical impact.
- Compatibility: Polyurethane coatings may be applied as a topcoat over epoxy primers to form a comprehensive and versatile protective system.
Inhibitive pigments
Inhibitive pigments are additives in protective coatings that retard or inhibit the action of corrosion. Examples are chromates and phosphates, which deposit corrosion-inhibiting agents over time to form a protective layer on the metal surface. Such chemicals are normally used in combination with epoxy and other resin-based coatings to build more general anti-corrosion performance.
Benefits
- Self-Healing Properties: The inhibitive pigments can repair minor damages because of the formation of protective film on the exposed metal areas.
- Long-term protection: these pigments ensure long-term corrosion resistance even in the most demanding applications, such as chemical plants and refineries.
Application of Industrial Coating Across Industries
Protective coatings, epoxy paints, and coatings are crucial where corrosion is a big issue in the industrial sectors. Some of the main applications where these coatings are applied include:
Oil and Gas Industry
Within the oil and gas sector, the pipelines storage tanks and offshore platforms are always exposed to corrosive substances- sea saltwater and chemicals as well as extreme temperatures. Protecting these through epoxy-based coatings prevents their failure, ensuring the integrity to critical infrastructure. Zinc-rich primers overlaid with polyurethane topcoats are some of the major applications in a multi-layered system for maximum protection.
Marine Industry
Ships, boats, and marine structures are always exposed to salt water and humidity with which the corrosion is accelerated. Protective coatings protect the ship hulls and decks against rust and wear and underwater surfaces against corrosion. Epoxy coatings, in combination with polyurethane topcoats, offer tough protection on ships in marine settings.
Chemical Plants
Chemical plants handle corrosive material that causes destruction to equipment and storage tanks. Epoxy-based coatings and coatings provide excellent resistance towards acids, alkalis and solvents, while epoxy-based coatings and coating give chemical plants a long protection period for machinery and containment systems. Inhibitive pigments in the coatings also enhance the corrosion resistance in those areas where chemical exposure is present.
Also Read: Difference Between Alkali and Alkaline & Their Demand in the Chemical Industry
Infrastructure and Construction
Protective coatings in steel structures, which are mainly exposed to bridges and buildings, prevent rust and degradation, especially when the environment around them is harsh. Epoxy and polyurethane coatings are used to protect metal infrastructures against corrosion abrasion from moisture salt and UV radiation for long-term preservation of infrastructure in coastal or industrial zones.
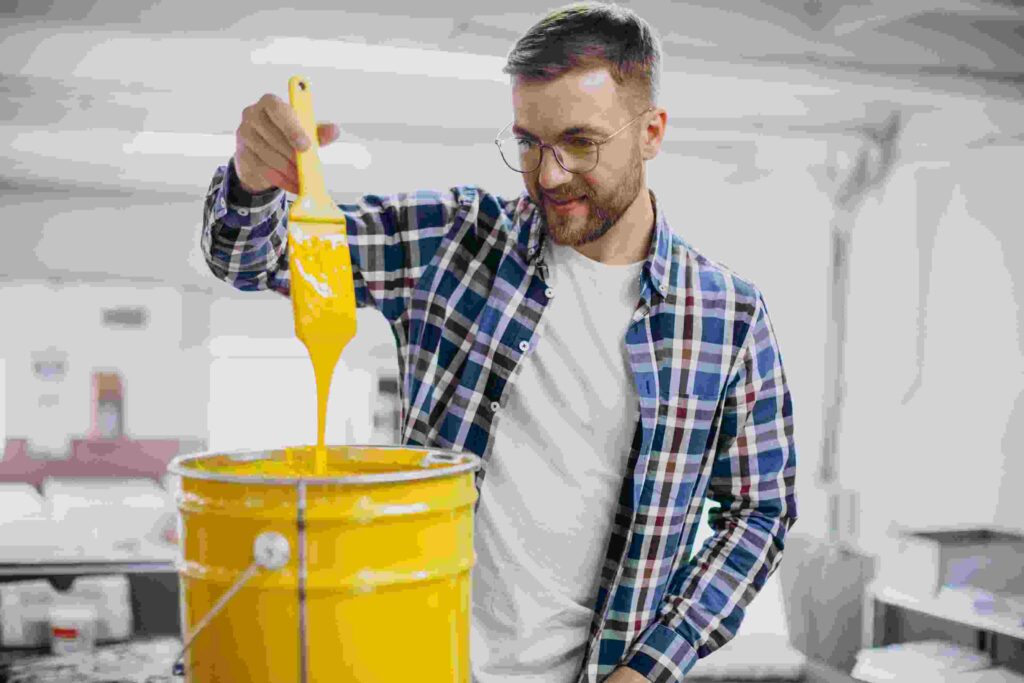
Evolution of Industrial Coatings
Protective coatings, particularly epoxy-based coatings have undergone extreme improvements regarding their level of corrosion resistance. However, they still have a long way to go. A major challenge affecting protective coatings is that they maintain their anti-corrosive functions over time, more so in facilities continuously exposed to harsh chemicals or extreme temperatures.
With these challenges in mind, coating technologies are being upgraded. Some of these emerging trends include:
- Nanotechnology: This mainly relates to using nanoparticles in protective coatings that exhibit enhanced corrosion resistance, mechanical strength, and self-healing properties.
- Environmentally Friendly Coatings: The higher level of environmental regulations is increasing the demand for coatings that offer a hazard-free aspect of being free from hazardous chemicals or VOCs.
- Smart Coatings: These coatings are environmentally responsive; they are either temperature or moisture-responsive. They can adjust their properties once exposed to an environment, making them dynamic coatings for corrosion protection.
Also Read: Vibrant Hues, Sustainable Solutions: Exploring India’s Organic Pigment Manufacturing Industry
Conclusion
Protective coatings, especially industrial epoxy paints and coatings, play a significant role in protecting materials against corrosion in grueling environments. With advanced chemicals, these coatings ensure durability and performance across many industries for a longer period. As technology advances, industrial coatings will continue to evolve, promising even more efficient and sustainable solutions for products in building resistance to corrosion.
Protect your equipment and infrastructure by using the advanced protective coatings from Elchemy. From epoxy-based coatings and paints, our solutions are designed to withstand harsh environments and last for years with perfect corrosion resistance. Secure the durability, safety, and performance of your asset base. Contact Elchemy today to explore the tailor-made coating solutions for meeting the needs of your industry.